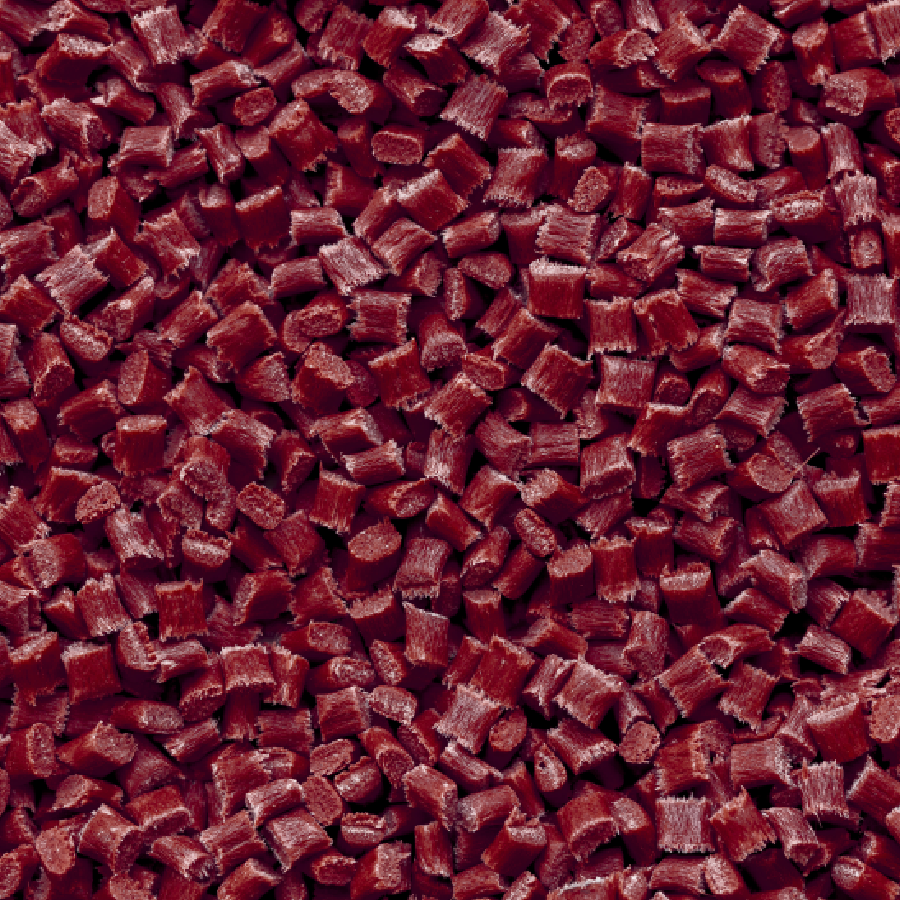
PPH Compounds
PP or polypropylene is a thermoplastic polymer used in many applications such as packaging and labeling, textiles (e.g. rope, thermal underwear and carpet), stationery, plastic parts and reusable containers, laboratory equipment, loudspeakers, automotive parts and polymer banknotes.
Polypropylene can be divided into three main groups:
- Homopolymer polypropylene (hPP) grades show high rigidity.
- Copolymer Polypropylene (cPP) grades provide better impact performance even at low temperature.
- Random Copolymer Polypropylene (raco PP) grades or statistical copolymers are transparent.
Polypropylene quality has improved over the years and will improve further in the future. The latest technological advances have created harder, clearer and more transparent grades and have taken market share from other polymers such as ABS and PS.
Another characteristic of polypropylene is its excellent chemical resistance to many chemical solvents, bases and acids.
PP is used in many applications, but its distinctive feature is its ability to produce hinges used in closures and CD/DVD slots.
Compounds:
- Unreinforced
- Glass Fiber Reinforced
- Glass Bead Reinforced
- Mineral Filled
- Flame Retardant
- Impact Resistant
- UV Resistant
- Heat Resistant
- Laser Markable
- Polypropylene can be processed in almost all available converting techniques.
- The main polypropylene applications are:
- Food packaging: cups, trays, ladles.
- Fiber extrusion.
- Furniture: garden chairs, tables.
- Household Goods: storage containers, boxes.
- Industrial packaging: detergent bottles, buckets and drums.
- Stoppers and caps.
Processes:
The melting process of polypropylene can be obtained through extrusion and moulding. Common extrusion methods include producing melt-blown and yarn-bonded fibres into long rolls, which are then converted and used to produce useful products such as face masks, filters, baby diapers and wet wipes.
The most common forming technique is injection molding, which is used for mugs, cups, cutlery, vials, lids, containers, utensils, household goods and automobile parts such as batteries. Techniques for air compression molding, including extrusion and molding processes, and injection stretch air compression molding are also used.
The specific molecular properties and the possibility of adjusting the level with additives used during production allow polypropylene to be used in a wide range of applications. For example, the addition of antistatic additives can help polypropylene surfaces to resist dust and dirt. Many dyeing techniques can be used in polypropylene, such as machining. Polypropylene parts can be surface coated to improve the adhesion of printer inks and dyes.